Interventional Care
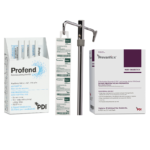
We notice that you are visiting us from . This site only services US-based visitors. Would you like to visit the site that is appropriate for your location?
It would be nice if there was just a “one-stop-shop” disinfectant that would do everything7:
Unfortunately there is no such disinfectant on the market as of yet, and so the Infection Preventionist finds him or herself in the frustrating position of ‘having’ and overseeing multiple disinfectants in their hospital or healthcare setting.
A typical phone call that an Infection Preventionist can relate to is “Our department just purchased this new, specialized piece of very expensive equipment and we need to know how to clean it…..TODAY. Please tell us what to do!” At this point the IP must scramble to come up with an acceptable disinfectant in a big hurry, and finds out that the manufacturer only has approved ONE particular type of disinfectant wipe for it or the warranty will be void. Why is this the case? Is it due to compatibility or is there another reason? Why has equipment compatibility become such a difficult task?
Every Infection Preventionist often bemoans the fact that they are, out of necessity, expected to be somewhat of a “subject matter expert” on surface compatibility when it directly relates to disinfection of that surface. Disinfection of the environment as well as medical equipment is a non-disputed fact of infection control and prevention of HAI’s in the hospital setting1. Repeated cleaning of shared patient equipment and areas of frequent use and turnover is par for daily routines in a hospital. However, choosing the right disinfectant that is also compatible with the surface being disinfected can be a very confusing endeavor. Choosing a disinfectant that degrades or corrodes a surface may not only incur expensive equipment replacement costs, but also an increased risk for infection as that surface begins to show mechanical and physical changes that can then harbor bacteria.
Compatibility Testing & HAI prevention:
Compatibility testing is a fascinating area of infection control and prevention that is not often focused on. Let’s look at the main points of compatibility testing as it relates to the ever increasing goals of preventing health care associated infections.
How is compatibility testing actually achieved? Anyone trying to become a subject matter expert in the area of medical device compatibility will run into the heart of the matter in a hurry; namely that there is no standardized method for manufacturer’s to determine compatibility, nor any sorts of predetermined parameters that manufacturers have agreed upon when determining if surface damage to their products has actually occurred because of a particular chemical or disinfectant.
The EPA defines “corrosive” as a “substance that eats or wears away materials gradually by chemical action”3. A truly compatible disinfectant would be one that does not cause changes to the mechanical and physical properties of that substance/material after repeated exposure. Optimally, this testing should (and needs) to be done in a real end-user type of setting to see what happens in true life, but this is almost never the case. Instead, manufacturers take the materials that make up their product (such as plastics and metals) and test them in a controlled laboratory setting. The most common testing method is to take a wipe and using a back and forth motion for 2 – 4 times wipe down the surface in question. This is repeated for between 120 – 200 cycles to mimic between 3 – 6 months of cleaning. On occasion they do not even test disinfectants, but rather just go with established and known chemical compatibility charts and choose a disinfectant they think will likely work the best.8 The reason behind this is that compatibility testing is actually very expensive, and manufacturers may not have the resources to do extensive testing on their products.
So, where does this leave the end user? Unfortunately the customer is ultimately at the mercy of manufacturers getting to pick and choose the disinfectant they use based on their own “internal” tests or opinions.
This leads to the next most obvious question, what shouldthe manufacturers be looking for in compatibility testing?When looking at compatibility testing here are the most obvious indicators of incompatibility:
Now that we have looked at the indicators of compatibility, what types of disinfectants are the most compatible with equipment on the market today. Research shows that alcohol with quaternary ammonium compounds are some of the most compatible, effective surface disinfectants on the market today. They cause relatively low amounts of changes in surfaces while having the advantage of being persistent if undisturbed, and working despite the presence of blood and body fluids.4 Quat- alcohol disinfectants do not damage surfaces the way oxidizing chemistries do6 and they are non-corrosive to metal pipes and other such materials5.
In conclusion, compatibility is an important area of infection control that can make a big difference in the prevention of healthcare associated infections. By becoming more knowledgeable around the key points of compatibility, the Infection Preventionist has one more weapon in their arsenal to fight the deadly pathogens that can so easily affect susceptible patients. Increased awareness around compatibility issues which will help to choose the right disinfectant for healthcare equipment can mean the difference between a good outcome or a poor outcome.